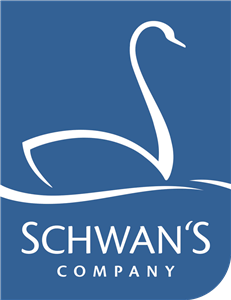
Job Information
Schwan's Company Engineering Change Coordinator in Marshall, Minnesota
At Schwan’s Company, the opportunities are real, and the sky is the limit; this isn’t just a job, it’s a seat at the table. Around here, every job matters, every voice counts, and every person contributes in a big way. As part of our front lines, we look to you to execute business, build relationships, and take pride in your work because at Schwan’s, you lead the way, and we value what you bring. Our passion is our food. Our secret is our people.
Schwan’s Company, a U.S. affiliate of the global lifestyle company, CJ CheilJedang Corporation, is a leading U.S. manufacturer and marketer of quality foods offered through retail-grocery and food-service channels. Our many popular brands include Red Baron®, Tony’s®, Big Daddy’s®, Villa Prima™ and Freschetta® pizza; Mrs. Smith’s® and Edwards® desserts; and Pagoda® and Bibigo Asian-style snacks. Schwan’s is a place for people with an appetite for more.
This Engineering Change Coordinator is responsible for assisting in the maintenance of engineering change documentation, product life-cycle management (PLM), and aiding in bill of material, routing and scrap auditing.
Responsibilities
Updates routings and bill of materials (BOMS) in SAP, compiles and audits data on scrap, prepares reports, charts, and other materials and ensures accuracy. Maintains files and keeps current on status of all projects.
Maintains SAP PLM master data including recipes and substances.
Responsible for creating and assigning change numbers to appropriate specifications based on the Engineering Change Number (ECN) request form ensuring all change information is accurate and complete prior to routing for approval and that the specification and the production system match prior to the change effective date.
Responsible for routing the specification in a timely manner and ensure final approval is complete. Creates and make changes to BOMs and Routings in SAP and ties them to SAP PLM. Maintains tracking records for all new products and changes made to products for manufacturing at the plant. Conducts weekly conference calls regarding new project/change tracking needs and communicates to the plant personnel the status of the projects and their timing.
Maintains MRP, Costed BOMS, and Tax, including speed and crewing for routings, within SAP for finished goods, WIPs, subassemblies, etc. utilizing the Product Developer, the Packaging Engineer, plant Manufacturing Manager, plant Continuous Improvement Manager, plant Scheduler, plant Cost Accountant, and Capacity & Inventory Control resources. Work closely with plant Manufacturing Manager and plant Cost Accountant to get MRP scrap rates updated on a regular basis
Responsible for Inventory Changeover Management including discontinuation, reformulations, and changeovers in materials for soft or hard cutovers working with plant Buyers, the Product Developer, and the Business Unit Marketing teams to ensure a smooth cutover on material usage and control. Ensures the planned transition is clear & precise between all participants & meets with our intended customer requirements/deliverables.
Monitors inventory levels of discontinued materials to ensure limited excess/risk of incremental material write-offs. Inactivates the BOMS, flags materials for deletion, and communicates to the Sr. Specification Coordinator.
Required to maintain a very high level of confidentiality and ensure effective communication between all departments all projects.
Performs all duties in compliance with State, Federal and company regulations, policies and procedures.
Responsible to conduct yourself and ensure your subordinates (if applicable) conduct themselves in a manner consistent with company mission, values, code of ethics, policies, and other standards of conduct.
Preferred Qualifications
Education: High School Diploma (or equivalent). Bachelor's degree preferred.
Years of Related Experience: 0-3 years. Previous experience in food industry and food production preferred.
Knowledge/Skills/Abilities: Ability to read and interpret documents such as safety rules, operating and maintenance instructions, and procedure manuals. Strong personal computer skills and knowledge of Windows, Word, Excel and SAP. Ability to write routine reports and correspondence. Must have strong attention to detail, organizational skills and self-motivation to work on multiple projects simultaneously. Ability to calculate figures and amounts such as discounts, interest, commissions, proportions, percentages, area, circumference, and volume. Ability to apply concepts of basic algebra and geometry. Willing to work in both office and production environment. Ability to speak effectively before groups of customers or employees of organization. Ability to apply commonsense understanding to carry out instructions furnished in written, oral, or diagram form. Ability to deal with problems involving several concrete variables in standardized situations. Good communication skills in dealing with all levels of management. Comply with all general safety policies and procedures, including using all required PPE (Personal Protective Equipment), in accordance with Company, Local, State and Federal Occupational Safety and Health Administration (OSHA)rules and regulations.