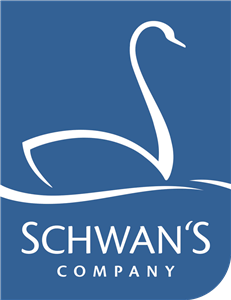
Job Information
Schwan's Company Principal Manufacturing Process Engineer in Saint Paul, Minnesota
Schwan’s Company, a U.S. affiliate of the global lifestyle company CJ CheilJedang Corporation, is a leading U.S. manufacturer and marketer of quality foods offered through retail-grocery and food-service channels. Its many popular brands include Red Baron®, Tony’s®, Big Daddy’s®, Villa Prima™ and Freschetta® pizza; Mrs. Smith’s® and Edwards® desserts; and Pagoda® Asian-style snacks. To learn more about Schwan’s, visit www.schwanscompany.com. The Principal Manufacturing Process Engineer, who will work within an hour of any of our plants/offices in Bloomington, MN; Stilwell, OK; Pasadena, TX; Salina, KS; or Florence, KY is responsible for improving manufacturing productivity by building technical skills to eliminate waste and increase efficiencies across the network. You will build a deep understanding of our food manufacturing phenomena in the teams, and leverage data to improve process variability and drive standardization. Thru technical leadership of the manufacturing team, R&D and capital engineering, the strategies you develop will be robust and result in net productivity to the Supply Chain. To note, we do require some level of specifically food manufacturing process engineering for this role. Key Responsibilities: + Develop enterprise-wide strategies to maximize manufacturing performance, capacity, and yield + Leads efforts to identify and drive productivity projects (yield/usage variance, raw material optimization, waste) including Strategic Projects + Creates and improves manufacturing instructions and standards to increase efficiency and reduce process variability + Collaborates with R&D, Manufacturing, and Project Engineering to develop process and equipment standards aligned with operations to ensure successful delivery and start-up of new initiatives + Develops advanced data analysis tools to expose and eliminate losses + Recognized as an expert in the processes used to manufacture our products and manufacturing standards utilization + Provides technical leadership to solve problems, drive improvements in processing systems and implement standards to ensure long term application. + Builds technical skills (math/science/physics) in operations to drive out losses in the manufacturing process. + Lead processes to audit standards and ensure conformance to lock in net productivity + Maintains a central library of manufacturing standards and instructions to provide sustainable source of technical skills and facilitate best practice sharing. + Engaged in food manufacturing forums and organizations to participate in industry wide standards and improvement strategies. + Responsible to conduct yourself and those you lead in a manner consistent with company mission, values, code of ethics, policies, and other standards of conduct Knowledge/Skills/Abilities: Years of Experience: 8+ years with some level of food manufacturing engineering required Education: Bachelor's degree in Mechanical, Chemical, Electrical, or Food Engineering (ABET accredited program preferred). - Leadership of structured problem solving approaches such as Lean, Six-Sigma, or TPM is preferred. - Experience with USDA, FDA, OSHA, EPA, requirements for manufacturing processes - Development of statistical models and data analytic tools using MS Excel, VB, SQL, Python are a plus. - Ability to travel 0 to 50% as required (dependent on location). - The desire to be able to follow our following four pillars: LEAD YOURSELF FIRST: You will leverage your deep expertise in our food manufacturing processes and build confidence in our operations to drive exceptional results. You will provide strategies and productivity commitments the supply chain can reliably count on. BE A DRIVING FORCE: You will define what supply chain excellence means because you have benchmarked the competition and know their strategies. You will be key in setting the road map and urgency to reduce our complexity, waste, and cost through everyday actions SHIFT OUR PARADIGM: You will leverage innovative technology to analyze large sets of data and design strategies needed to drive manufacturing performance. You provide the technical leadership required to act when the path forward is ambiguous or hard for others to see. ONE TABLE ONE TEAM: You will set the table for unrivaled productivity by building partnerships internally and externally to deliver the best manufacturing practices. You will foster an environment where the team is able to challenge each other and celebrate the successes together. This job description is not intended to be an exhaustive list of all duties, responsibilities and qualifications associated with the job. An individual must be able to perform all of the duties and responsibilities listed in a fully competent manner to be considered successful in the job. Reasonable accommodations may be made to enable individuals with disabilities to perform essential duties and responsibilities.